The History of Warehouse Maturation
Contents
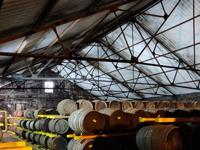
The history of whisky production is closely linked to law, taxation and the attempts of distillers to avoid the latter. Taxation dates back to 1643 in Ireland and 1644 in Scotland. A state license for distilling whisky has been required in Ireland since 1661, and in Scotland since 1707. The number of illegal distilleries throughout history has far exceeded the number of legal ones. That changed in Scotland with the Act of Excise 1823. This law simplified taxation. At the same time, a minimum size of the still was set at 40 gallons (approximately 182 liters). Most of the distilleries, however, were still small farm distilleries, many with only one pot still.
What is a Dunnage warehouse?
Similar to Ireland at that time, many distilleries in Scotland also sold the freshly distilled whisky directly on. The wooden casks were used primarily as a means of transport. Depending on the location of the distillery on an island, on a canal or on a railway line, the filled barrels had to be stored for a few days or weeks before they could be removed. So gradually the first small warehouses were built, but they were rarely able to hold large quantities of barrels. The first cask warehouse we know of was built at the Bowmore Distillery on Islay and is still in use today.
Many distilleries were built in such a way that they used the natural gradient in the area for production. In this way, the liquids were able to run through production step by step, following the force of gravity. The warehouses were often located at the deepest and often the wettest point on the site.
The introduction of continuous distillation
With the continuous column distillation plant, patented by Robert Stein in 1826, the distilleries were able to increase production volumes significantly. With this method it was possible to process unmalted grain. In 1832 this process was optimized again by Aeneas Coffey as the Coffey still. As production increased, so did the number and size of warehouses.
With the introduction and spread of blended scotch from 1850, i.e. the mixing of malt and grain whisky, the demand for Scottish whiskey continued to increase. The blenders bought the whiskey from many distilleries and stored it in their own warehouses. At times in Scotland over 90% of whiskey matured in the warehouses in Edinburgh harbor, where many blend manufacturers and dealers had their warehouses. From 1880 there was a real whiskey boom and many new distilleries were built in Scotland. This boom almost came to a standstill in 1898, partly due to the bankruptcy of the then largest whiskey blender, Pettison. In the period that followed, the distilleries began to build their own warehouses on a larger scale.
Mandatory maturation
It was not until the Immature Spirits (Restriction) Act of May 19, 1915 that the minimum storage of two years for whisky under bond was introduced in Great Britain (thus also in Scotland and Ireland), which was increased to three years 12 months later. This minimum age for whisky came about as a result of the same forces that mandated a minimum 40% ABV (Alcohol by Volume) namely:
- the prohibitionists of the early 20th century
- a staunch abstainer (David Lloyd George) as British Finance Minister
- the grain shortages in the aftermath of war
Early Dunnage warehouses
The first warehouses to be built in Ireland and Scotland were the Dunnage Warehouse . Depending on the location and the space available, these warehouses were built with one or two storeys. Later and in the big cities with up to six or more storeys high.
The buildings had exterior walls made of natural stone or brick up to a meter thick. The lowest storey was laid out at ground level and, as a rule, did not have a paved stone floor. The individual intermediate ceilings of the floors consisted of iron girders and wooden beams, which were provided with wooden planks. The wooden planks were laid in such a way that the air in the buildings could slowly rise through narrow gaps. The roofs were covered with slate or stone slabs. The thick outer walls and the open earth or gravel floor ensured a rather constant, cool, humid camp climate. As the number of storeys increases, the microclimate changes upwards to become warm and dry.
On the rather flat floors of the Dunnage Warehouses, the barrels are stacked horizontally, separated by wooden beams, in two or three layers depending on the cask size. This makes it possible to combine barrels of different sizes in storage: Sherry Butts in the bottom layer, Hogsheads and Quater Casks in the third layer above. A downside to this is that getting access to lower barrel requires all barrels above being relocated. Even today, with the help of a forklift truck, this is still a complex, time-consuming job. In the past, this was a real back-breaking job, only with the help of movable wooden ramps and lots of warehouse work. Many dunnage warehouses are still to small to fit large machinery and so while many of these old warehouses still stand today, they are rarely used for whiskey maturation.
Dunnage warehouses are still being built today however, these modern dunnage warehouses can only be compared to the old ones to a limited extent. As a rule, these are steel-frame halls clad with sheet metal, like all other modern whiskey warehouses. Only the flat construction and the partly open ground have remained. The storage climate is therefore often different. In particular, the temperature fluctuations are significantly greater.
Racked warehouses in North America
In North America, this storage method was quickly abandoned. In contrast to Ireland and Scotland, there was no shortage of woodand virtually no barrels from Europe. Thus, the barrels were made directly for whiskey maturation making it possible to determine the dimensions for the barrels in advance. This made it possible to build storage racks made of wood for the barrels, which were clad with sheet metal on the outside. With the help of simple mechanical chain lifts it was also possible to lift the barrels to greater heights. So the warehouses grew taller. These racked warehouses emerged and with them the American Standard Barrel.
Due to the very high temperature differences between the upper and lower floors, especially in the summer months in Kentucky and Tennessee, a rotary bearing was developed. The freshly filled barrels were placed in the topmost layer and moved downwards layer by layer in the building over time. This allowed the whiskey to mature evenly. Nowadays this relocation is no longer the norm and distilleries rely upon blending casks mixed from various layers to ensure consistancy. In the big cities and in Canada, these wooden shelves were given solid exterior walls made of brick.
Racked warehouses in Europe
With the invention of the iron framework, the warehouses began to be adopted in Scotland and Ireland. The spans of the roofs became considerably larger and the first storage racks made of iron frameworks began to be built into the converted, wider warehouses. These were generally comprised of four layers with the uncovered ground of the Dunnage warehouses being retained. One of the first distilleries to be remodeled in this way was Blair Athol, a crucial producer of Bells.
As a result of ongoing technical progress in particular the invention of the forklift the height of rack warehouses continued to climb following the Second World War. DCL (Distillers Company Ltd. today’s Diageo) pushed ahead with the modernization of the production facilities and the warehouses. At the same time transitioning to the use of only two cask sizes; butt and hogshead. DCL began to build new, large standardized warehouses at a mulltiple locations around 1960, with storage racks only for these two barrel sizes. At Cambus distillery alone, 51 new warehouses were built in Blackgrange Bond, each with a capacity of around 70,000 hogsheads. Another 47 identical warehouses were built at five other locations. The largest warehouses of this type in Scotland can currently accommodate up to 90,000 cask. Around 60% of all casks currently maturing distillate in Scotland are stored storage in this way.
Palletised storage warehouse
In Canada around 1960 racked warehouses proved insufficient flexibility for expansion rates and the search for alternatives storage methods began. Shelving systems were dispensed with and the barrels were placed upright on storage pallets. On these 6 filled barrels were clamped together with a steel band, so that they could be moved quickly and easily with a larger forklift truck. These pallets were stacked on top of each other in a huge palletized warehouse. The pioneer and driving force here was Seagram with its Hiram Walker distillery in Walkerville. Around twenty minutes from the distillery, a vast warehouse complex was built with 64 warehouses, built in blocks of four spread out over some 160 football (or ice hockey) fields. Each warehouse can hold around 32,000 barrels.
In Ireland, Irish Distillers and John Teeling adopted this storage method. Virtually all new large warehouses built in Ireland after 1985 operate on the method. The first warehouses of this type were built in Scotland around the same time. Here, too, Seagram was the pioneer via her Scottish arm Chivas, as well as William Grant & Sons and Macdonald & Muir. The largest warehouses of this type in Scotland today have a floor space of 10,000 square meters, are divided into several storage cells and can hold up to 120,000 cask.
In the USA, the first warehouses of this type were not built until after 2005, but some companies have returned to rackhouses. Today, in Canada and Ireland, more than 90% of the barrels stored with maturing distillate are on pallets. In Scotland Palletised storage warehouses now account for 36%-40% of all whisky currently maturing
Classic warehouses
While the Dunnage Warehouse is by far the oldest design of a whiskey warehouse, it is not the only classic warehouse type. The racked warehouse has been used successfully in Scotland for more than four generations, and in some cases for over 150 years in the US. Whether pallet storage should be described as a ‘modern method’ after some 50 years of history is also worth pondering.
What is certain is that the individual types definitely have an influence on the maturation of the distillate. However, this influence is clearly overestimated. Rather, an interplay of many factors, such as barrel size, alcohol strength, location of the warehouse, the design of the warehouse and the local climatic conditions, is decisive.